Металургія є одним з найбільших споживачів первинних енергоносіїв в українській промисловості. Якщо у розвинених європейських країнах на виробництво однієї тонни чавуну витрачають близько 450 кг умовного палива, то в України -650 кг. Не кажучи вже про випуск прокату, де вітчизняні норми практично вдвічі вище західних. Шляхи скорочення енерговитрат давно відомі та апробовані: в першу чергу - це заміна мартенівського способу виплавки сталі на киснево-конвертерний. На жаль, в Україні до цього часу близько половини (46%) всієї стали отримують мартенівським способом.
Чому конвертери
Лідируючі позиції серед відомих способів масового виробництва сталі киснево-конвертерний процес займає завдяки відсутності витрат палива. Тут для отримання сталі використовується не дефіцитний на Україну природний газ, а кисень, одержуваний з повітря, пропущеного через спеціальний розділовий блок.
Вперше у світовій практиці кисень для продувки чавуну був застосований радянським інженером Н.І. Мозговим на київському машинобудівному заводі `Більшовик` в 1933 році. У промисловому масштабі киснево-конвертерний процес вперше був випробуваний в Австрії в 1952 році. А в СРСР перший киснево-конвертерний цех (ККЦ) був введений в експлуатацію в Дніпропетровську на металургійному заводі ім. Петровського в 1956 році.
З тих пір киснево-конвертерний спосіб отримання сталі став ведучим, поступово витіснивши раніше лідирує мартенівський. Сьогодні даний спосіб забезпечує більшу частину світового виробництва сталі. І не дивно, адже його техніко-економічні переваги в наявності. Серед них - більш висока продуктивність на одиницю виплавленої сталі, менші капітальні витрати, більш сприятливі умови для механізації і автоматизації виробничих процесів і суміщення процесу виплавки сталі з її безперервної розливанням. При цьому, киснево-конвертерний спосіб можна переробити чавун практично будь-якого складу і отримувати широкий сортамент сталей, включаючи леговані.
Що маємо
В Україні в даний час діє сім киснево-конвертерних цехів (металургійні комбінати `Arcelor Mittal Кривий Ріг`, `Азовсталь` `ММК ім. Ілліча`, `ДМК ім. Дзержинського` і `ДМЗ ім. Петровського`, Єнакіївський і Алчевський металургійні заводи ). У них налічується 21 конвертер, за допомогою яких отримують трохи більше половини всієї української сталі. Однак до повної заміни мартенів конвертерами ще далеко. Однак зниження частки мартенівського виробництва хоча б до 15% дозволить економити близько 1,45 млрд. куб. м газу на рік.
Сьогодні ключові позиції з виробництва сталі киснево-конвертерний спосіб займають меткомбінати `Arcelor Mittal Кривий Ріг` і `Азовсталь`. На Криворізькому комбінаті перший конвертер ємністю 35 тонн був введений в експлуатацію ще в 1957 році, одним із перших у нашій країні. Сьогодні ж виробнича потужність конвертерного цеху підприємства сягає 5,4 млн. т сталі на рік. До складу цеху входять шість 160-тонних конвертерів (2 блоку по 3 конвертера).
Близько двох років тому на підприємстві був прийнятий інвестиційний план з модернізації комбінату, який передбачав будівництво нового конвертерного цеху з двома конвертерами загальною продуктивністю 5,2 млн. т на рік. Реалізація проекту дозволила б вивести з експлуатації застарілі мартенівські печі і ДСПА сумарною продуктивністю близько 2 млн. т на рік. Однак через кризу реалізація його була припинена, сьогодні проект знаходиться в режимі очікування.
Найбільші в країні конвертери функціонують на `Азовсталі`. У киснево-конвертерному цеху, введеному в експлуатацію в 1977 році, сьогодні працює два конвертери по 330 тонн, річний номінальний обсяг виробництва становить 4,5 млн. т. Розробленою кількома роками раніше програмою модернізації заводу була передбачена повна реконструкція конвертерного цеху і будівництво третього конвертера . Реалізація проекту допомогла б збільшити потужності підприємства по сталі до 8 млн. т на рік і закрити існуючу мартенівське виробництво продуктивністю до 2 млн. т на рік.
До теперішнього часу в рамках даної програми встигли здійснити лише капітальний ремонт конвертера № 1 із заміною корпусу (інвестиції в проект склали понад 20 млн. грн.). Ремонт другого конвертера і будівництво третього відкладені `до кращих часів`.
Нездійснені проекти
До кризи програми модернізації, що включали, зокрема, будівництво конверторних цехів з повним виведенням з виробництва мартенівських печей, були розроблені і на інших меткомбінатах країни.
Так, на ММК ім. Ілліча був опрацьований проект реконструкції сталеплавильного виробництва з метою заміни застарілих мартенівських печей на конвертери. Проектом передбачалося будівництво трьох 160-тонних конвертерів потужністю близько 1,2 млн. т кожний, які повинні були замінити мартени сумарною потужністю до 4 млн. т на рік.
До теперішнього часу, за словами начальника відділу автоматизованого електроприводу, електропостачання та АСУ ТП АТЗТ `Важпромавтоматика` Олександра Петровича Даніліна, який безпосередньо брав участь у розробці та впровадженні проекту реконструкції сталеплавильного виробництва комбінату, два конвертери вже введені в експлуатацію, роботи по третьому через неможливість фінансування поки відкладені. Проте керівництво підприємства з упевненістю заявляє, що вже в цьому році планується відновлення робіт з переходу на киснево-конвертерне виробництво.
Розмови про заміну мартенівського методу на конвертерне велися також на Макіївському МЗ, де сталь виплавлялася виключно мартенівським способом. Так, в рамках програми реконструкції СПК до 2011 року тут планувалося побудувати новий конвертерний цех, що дозволило б вивести з експлуатації чинне мартенівське виробництво. Потужність комплексу планувалася на рівні 5 млн. т на рік. Проте реальні інвестиції були мінімальними, їх ледве вистачало на підтримку наявного технічного рівня метзаводу, що відсунуло будівництво ККЦ на невизначений термін.
Лише на Алчевському МК незважаючи на кризу вдалося втілити запланований перехід від мартенів на киснево-конвертерне виробництво.
Наочний приклад
Будівництво ККЦ на Алчевському меткомбінаті вважається найбільш значущим інноваційним проектом в Україні за останні кілька років. Не дивно, адже останній сталеплавильний комплекс у нашій країні був побудований більше 25 років тому.
На Алчевському МК будівництво киснево-конвертерного цеху почалося ще в 2006 році. Проектом передбачалося будівництво двох конвертерів ємністю 300 тонн кожен з відповідною інфраструктурою: відділення переливання та десульфурації чавуну, проліт перестановки шлакових чаш, відділення перевантаження та зважування металобрухту, ділянка підготовки, зберігання і транспортування сипучих матеріалів, комплекс газоочисних споруд і кисневий цех. Загальна продуктивність ККЦ складає до 5,5 млн. т на рік. Тривалість плавки від випуску до випуску - 40 хвилин. Середньодобова продуктивність (з урахуванням загальної кількості плавок в рік і повного робочого часу) при роботі обох конвертерів - 58 плавок. Постачальником обладнання і технологій для нового цеху виступила австрійська фірма Siemens-VAI, генеральною проектною організацією - НДІ `Діпросталь` НТЦ `Енергосталь`, генпідрядником будівельно-монтажних робіт - ТОВ ПБП `Азовінтекс`.
Будівництво здійснювалося рекордно швидкими темпами і не мало світових аналогів. Вже в кінці 2007 року був введений в експлуатацію перший конвертер потужністю 3 млн. т на рік. У 2008 році комбінат закінчив будівництво другої черги і запустив другий конвертер.
Сьогодні до складу ККЦ крім конвертерів входять двопозиційний агрегат піч-ківш, вакууматор камерного типу та дві двухручьевие слябової МБЛЗ номінальною потужністю 2,5 млн. т на рік кожна, запущені в 2005 і 2006 роках відповідно. Загалом перехід на ККЦ тривав близько 5 років і коштував `Індустріального Союзу Донбасу` більше $ 1 млрд.
Життєва необхідність
В даний час виключно мартенівським виробництвом, крім Макіївського МОЗ, мають у своєму розпорядженні `Запоріжсталь`, Донецький МЗ і `Інтерпайп Нижньодніпровський ТПЗ`.
При цьому, безумовним лідером мартенівського виробництва в країні залишається запорізький меткомбінат, що значно підриває його конкурентоспроможність, так як собівартість виплавки сталі в мартенах на 10-15% вище конвертерної через велику енерго-і ресурсовитратності, а також значних втрат продукції при виробництві.
Цікаво, що підприємство почало планувати перехід на конвертерний спосіб виробництва сталі ще в 2003-2004 роках. А в 2008 році був підписаний контракт з Siemens-VAI про закупівлю обладнання для майбутнього ККЦ, який вступить в силу після першого надходження платежу з української сторони.
У цілому даний інвестиційний проект `Запоріжсталі` передбачає будівництво двох конвертерів продуктивністю 250 тонн кожен, двох установок десульфурації чавуну, вакууматора і двох толстослябових МБЛЗ. У новому цеху передбачається виробництво 4,7 млн. т сталі на рік. Продуктивність ККЦ розрахована так, щоб потужності доменного цеху використовувалися максимально: чотирма печами буде виплавлятися 4 млн. т чавуну на рік.
За оцінками керівництва комбінату, перехід на конвертерний метод дозволив би не тільки підвищити продуктивність і знизити витратність виробництва, але і забезпечити виплавку сталі з вузькими межами змісту елементів, поліпшити якість поверхні прокату, однорідність структури і властивостей металу. Крім того, передбачалося, що `Запоріжсталь` після будівництва ККЦ зможе помітно розширити марочний сортамент сталей, освоївши випуск, зокрема, трубних марок, якісної конструкційної сталі, сталі підвищеної міцності, стали для судин і котлів, що працюють під тиском, а також стали для штампування (в тому числі, для автомобілебудування).
Реалізація проекту також повинна була дати підприємству можливість отримувати не тільки високоякісний гарячий прокат, але і холоднокатаний лист, а також продукцію четвертого переділу (щорічно до 300 тис. т `оцинковки` і листа з полімерним покриттям). Крім того, передбачалося знизити втрати стали в обрізу на 110 кг / т.
Але, незважаючи на всі переваги киснево-конвертерного виробництва з початком фінансової кризи керівництво і власники комбінату в черговий раз заморозили будівництво ККЦ. Це й зрозуміло, адже вартість даного проекту, розрахованого на тривалий період реалізації, може скласти більше $ 1 млрд.
У чому причина?
В даний час для вирішення найбільш нагальною проблеми металургійної галузі - її енерговитратності і сильною енергозалежності українському гірничо-металургійному комплексу необхідна докорінна модернізація, пріоритетним напрямком якої залишається перехід до конвертерного виробництва сталі і повна відмова від мартенів. Проте практично всі такі інвестиційні проекти, які були розпочаті до кризи, припинені через відсутність коштів.
В даний час діють кілька видів пільг для промислових підприємств, які впроваджують енергозберігаючі технології. По-перше, це можливість безмитного ввезення енергоефективного обладнання без сплати ПДВ. За інформацією Національного агентства з ефективного використання енергоресурсів (НАЕР), станом на початок 2010 року цією пільгою скористалися понад 50 підприємств різних галузей і регіонів. По-друге, для компаній, які впроваджують енергоефективні технології, існує можливість платити тільки половину податку на прибуток. Нормативна база для цього була оформлена ще в квітні 2008 року. Однак на сьогодні цієї преференцією поки не скористалося жодне підприємство. У найближчому майбутньому планується прийняття ще однієї постанови, стимулюючого впровадження енергоефективних технологій - можливість прискореної амортизації ввезеного в Україні енергозберігаючого обладнання.
Однак очевидно, що перерахованих заходів поки недостатньо, і металургійні підприємства сьогодні гостро потребують загальну державну програму стратегічного розвитку. Саме її реалізація повинна стати пріоритетним напрямом діяльності уряду в металургії.
Ольга Фоміна
http://www.rusmet.ru/
Труднощі в переході до сучасних технологій виплавки сталі в Україні
+380 44 237 XX XX +380 44 237 2567
Ідентифікатор: 8049
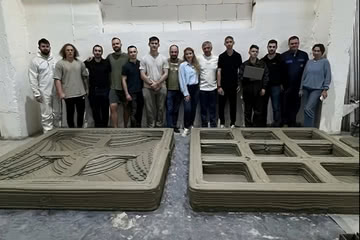
21 трав. 2025 р.